The Essential Role of Chemicals Used in Sugar Processing
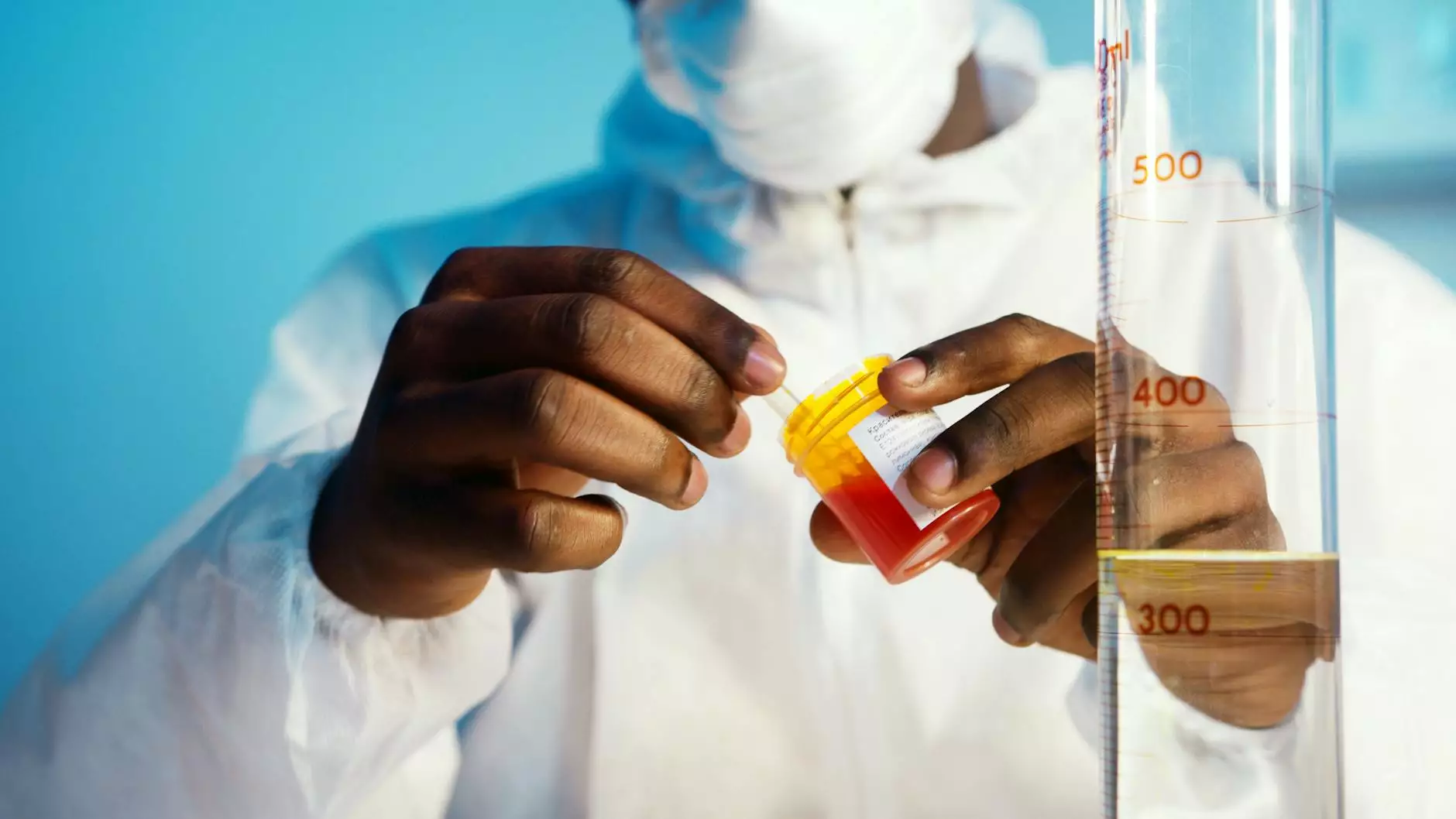
Sugar processing is an intricate and vital business sector that forms the backbone of numerous food and beverage industries. The journey from sugarcane or sugar beet to refined sugar involves several steps, each requiring specific chemicals to optimize the process. This article delves into the various chemicals used in sugar processing, their purposes, and the implications of their usage for quality control and sustainability.
Understanding Sugar Processing
To appreciate the role of chemicals in sugar processing, it is crucial to understand the overall process itself. Sugar can be derived from two primary sources: sugarcane and sugar beets. The processing involves key stages including extraction, purification, and crystallization. During each stage, different chemicals are utilized to enhance the efficiency and quality of the sugar produced.
1. Extraction Stage
The extraction of juice from sugarcane or sugar beets typically involves the use of water, which is considered the most fundamental solvent in this process. However, to improve the extraction efficiency, various chemicals play a significant role:
- Acids: Hydrochloric acid or sulfuric acid may be used to adjust the pH levels of the juice, optimizing the extraction process.
- Enzymes: Pectinase and cellulase help in breaking down plant cell walls, facilitating the release of juice.
- Antioxidants: Ascorbic acid is employed to prevent oxidation of the juice, preserving its quality during processing.
2. Purification Stage
After extraction, the juice contains a plethora of impurities, such as color, pH, and fibrous materials. Purification is crucial to yield high-quality sugar. Here, additional chemicals are used:
- Lime (Calcium Hydroxide): This is added to raise the pH and precipitate impurities. The resulting sludge is then removed, allowing for clearer juice.
- Phosphoric Acid: Sometimes used in conjunction with lime, it helps in the clarification of sugar juice.
- Activated Carbon: Employed to remove colorants and additional impurities from the juice, ensuring the final sugar product is of high quality.
3. Crystallization Stage
The crystallization phase is where sugar is formed from the clarified juice. It’s a critical point in the manufacturing process. Here are some of the key chemicals used in sugar processing during crystallization:
- Invert Sugar: A mixture of glucose and fructose, invert sugar can prevent crystallization and result in a smoother sugar product.
- Seeding Agents: Fine sugar crystals are introduced into the syrup to initiate crystallization. These agents promote uniform crystal growth.
- Antifoaming Agents: These chemicals reduce foaming during boiling, ensuring a consistent cooking process.
The Importance of Quality Control
Quality control in the sugar processing industry is paramount. The use of precise quantities of chemicals directly correlates to the quality of the final sugar product. Moreover, continuous monitoring of pH, temperature, and the concentration of various reactants ensures that production remains within desired parameters.
Environmental Considerations
With increasing scrutiny over environmental impacts, sugar processing businesses are now focusing on reducing their chemical footprint. Many companies are investing in advanced technologies that minimize the use of hazardous chemicals while ensuring the quality of the sugar remains intact.
Impact on Sustainability
As the world moves towards more sustainable practices, the sugar industry is responding by exploring green chemistry alternatives. Sulfite and phosphoric treatments are being replaced by more eco-friendly options that reduce environmental impact while maintaining efficiency. Additionally, the adoption of bio-based chemicals is on the rise, showcasing the industry's commitment to sustainability.
Integration with Water Purification Services
In the context of sugar processing, water purification services play an integral role. Clean, safe water is critical for various processes, including extraction and washing of sugarcane or beets. Companies like Bimak Skimya are pivotal in providing effective water purification solutions, ensuring that the water used in sugar processing meets stringent quality standards. The purification process includes:
- Filtration to remove particulate matter.
- Chemical treatment to eliminate contaminants.
- Reverse osmosis for further purification.
The Future of Sugar Processing Chemicals
As the sugar processing industry evolves, the demand for innovative solutions to enhance efficiency and minimize environmental impact continues to grow. The future will likely see:
- Increased use of bio-based chemicals that are non-toxic and environmentally friendly.
- Automation and advanced monitoring systems for precise control over chemical usage.
- Collaborations with water suppliers to ensure a continuous supply of high-quality water.
Conclusion
The role of chemicals used in sugar processing is undeniable; from extraction through purification to crystallization, these chemicals are essential. The industry is now moving towards more sustainable practices that respect both environmental and health standards. By focusing on innovative solutions, sugar processing can align with global sustainability goals while continuing to produce the high-quality sugar that is essential to our daily lives.
For businesses on a quest for excellence, understanding the critical role of chemicals in sugar processing and investing in reliable water purification services can define their path to success in an ever-evolving market.
chemicals used in sugar processing