The Essential Role of Die Casting Parts in Modern Manufacturing
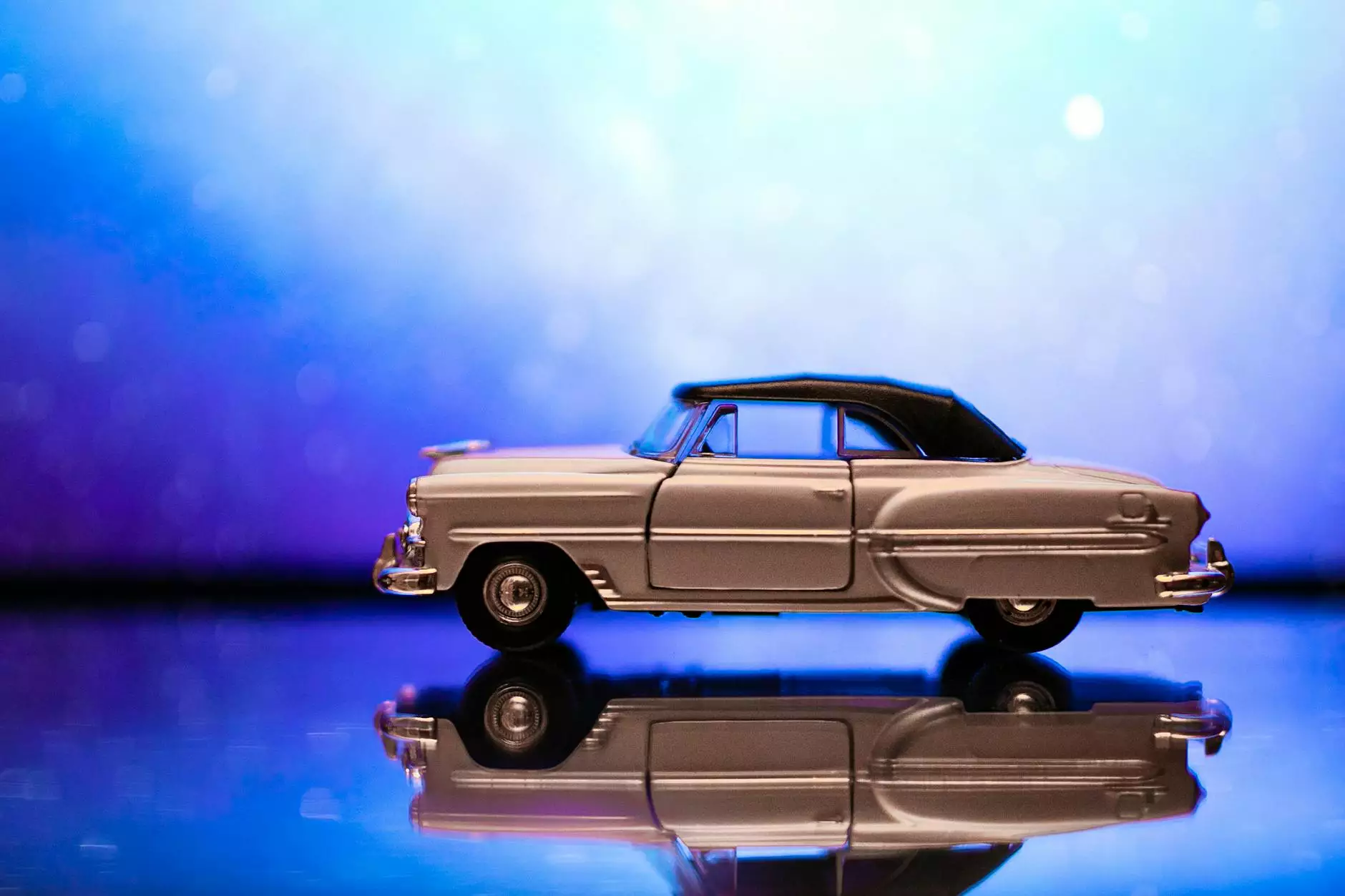
As we delve into the realm of today's manufacturing landscape, it's crucial to understand the importance of die casting parts. These components have revolutionized how industries operate, providing unmatched efficiency and precision. This article aims to explore the myriad advantages of die casting parts, their applications, and their integral role in the manufacturing sector, particularly for metal fabricators.
Understanding Die Casting: A Brief Overview
Die casting is a manufacturing process characterized by forcing molten metal into a mold cavity. This method enables manufacturers to create complex shapes with high dimensional accuracy and smooth surfaces. The key materials commonly employed in die casting include:
- Aluminum
- Zinc
- Magnesium
- Copper
The ability to use various metals allows die casting parts to serve multiple industries, including automotive, aerospace, electronics, and consumer products.
Advantages of Die Casting Parts
Die casting offers several advantages that make it a favored technique among metal fabricators. Here are some of the most compelling benefits:
1. High Production Efficiency
One of the standout features of die casting parts is their ability to be mass-produced with high efficiency. The die casting process allows for:
- Rapid production cycles that minimize lead times.
- Low per-unit costs, making it economical for high-volume runs.
- Reduced labor costs through automation and simplified processes.
2. Exceptional Precision and Repeatability
In an industry where precision is paramount, die casting parts shine. The process boasts:
- Tight tolerances that ensure consistency across all produced parts.
- Smooth finishes that may require minimal post-processing.
- Reduced risk of defects, leading to fewer product recalls and increased customer satisfaction.
3. Design Flexibility
Die casting allows for complex geometries that are often difficult or impossible to achieve using other methods. Designers can take advantage of:
- Thin walls for weight reduction.
- Complex shapes that optimize the performance of the final product.
- A variety of surface finishes that enhance aesthetic appeal.
4. Enhanced Material Properties
Components created through the die casting process have superior mechanical properties due to the high pressure used during molding. Key benefits include:
- Increased strength and durability against wear and corrosion.
- Improved thermal and electrical conductivity for specific applications.
Applications of Die Casting Parts
Die casting parts are utilized across various industries, reflecting their versatility. Some notable applications include:
Automotive Industry
The automotive sector extensively relies on die casting for producing intricate components such as:
- Engine blocks
- Transmission housings
- Structural components
Aerospace Sector
Aerospace components demand high precision and reliability. Die casting fulfills these requirements through parts like:
- Casings for engines
- Brackets and fixtures
- Support components that adhere to strict safety standards
Electronics Manufacturing
The electronics industry benefits from die casting parts by using them in applications such as:
- Enclosures for devices
- Heat sinks
- Housing for intricate electronic devices
Consumer Products
In the realm of consumer goods, die casting parts are common in:
- Appliances
- Hardware such as locks and latches
- Decorative items and fixtures
The Die Casting Process: A Step-by-Step Guide
Understanding the breadth of die casting parts also requires a closer look at the die casting process itself. Here’s a detailed overview:
Step 1: Design and Engineering
The journey begins with the design phase, wherein engineers create detailed CAD models. The designs focus on:
- Minimizing material waste
- Ensuring manufacturability
- Meeting tolerance specifications
Step 2: Mold Creation
Once finalized, molds are created using high-quality steel or aluminum, designed to withstand the pressures of die casting.
Step 3: Melting Metal
The selected metal is then melted in a furnace. Maintaining optimal temperature is crucial to ensure the metal flows smoothly into the mold.
Step 4: Injection
Once molten, the metal is injected into the mold at high pressure, forcing it to fill the cavity completely. This step is pivotal in achieving the desired precision.
Step 5: Cooling and Solidification
The injected metal cools and solidifies, taking the shape of the mold. Proper cooling times are essential to avoid defects.
Step 6: Ejection
After solidification, the mold opens, and the finished part is ejected. Quality inspections follow to ensure all specifications are met.
Environmental Considerations in Die Casting
As industries become more aware of their environmental footprint, die casting has adapted to incorporate sustainable practices. Key considerations include:
- Recycling: Many die casting metals, especially aluminum, are highly recyclable.
- Energy-efficient processes that reduce waste and energy consumption.
- Adopting eco-friendly practices throughout the supply chain.
Choosing the Right Metal Fabricator for Die Casting Parts
When selecting a metal fabricator for your die casting needs, consider the following criteria:
- Experience and Expertise: Look for manufacturers with a proven track record in die casting.
- Quality Assurance: Ensure they have robust quality control processes to maintain standards.
- Technological Capabilities: The latest technology can enhance production efficiency and product quality.
Conclusion
In conclusion, die casting parts play an indispensable role in modern manufacturing, offering significant advantages in efficiency, precision, and adaptability. As industries continue to evolve, the demand for high-quality die cast components will only increase. Choosing the right partner for your metal fabrication needs is essential to harness the full potential of this versatile manufacturing process.
For businesses looking for quality die casting parts, partnering with experienced professionals such as those at deepmould.net can pave the way for enhanced production capabilities and product excellence.