The Evolution and Importance of **Automotive Plastic Parts** in Modern Manufacturing
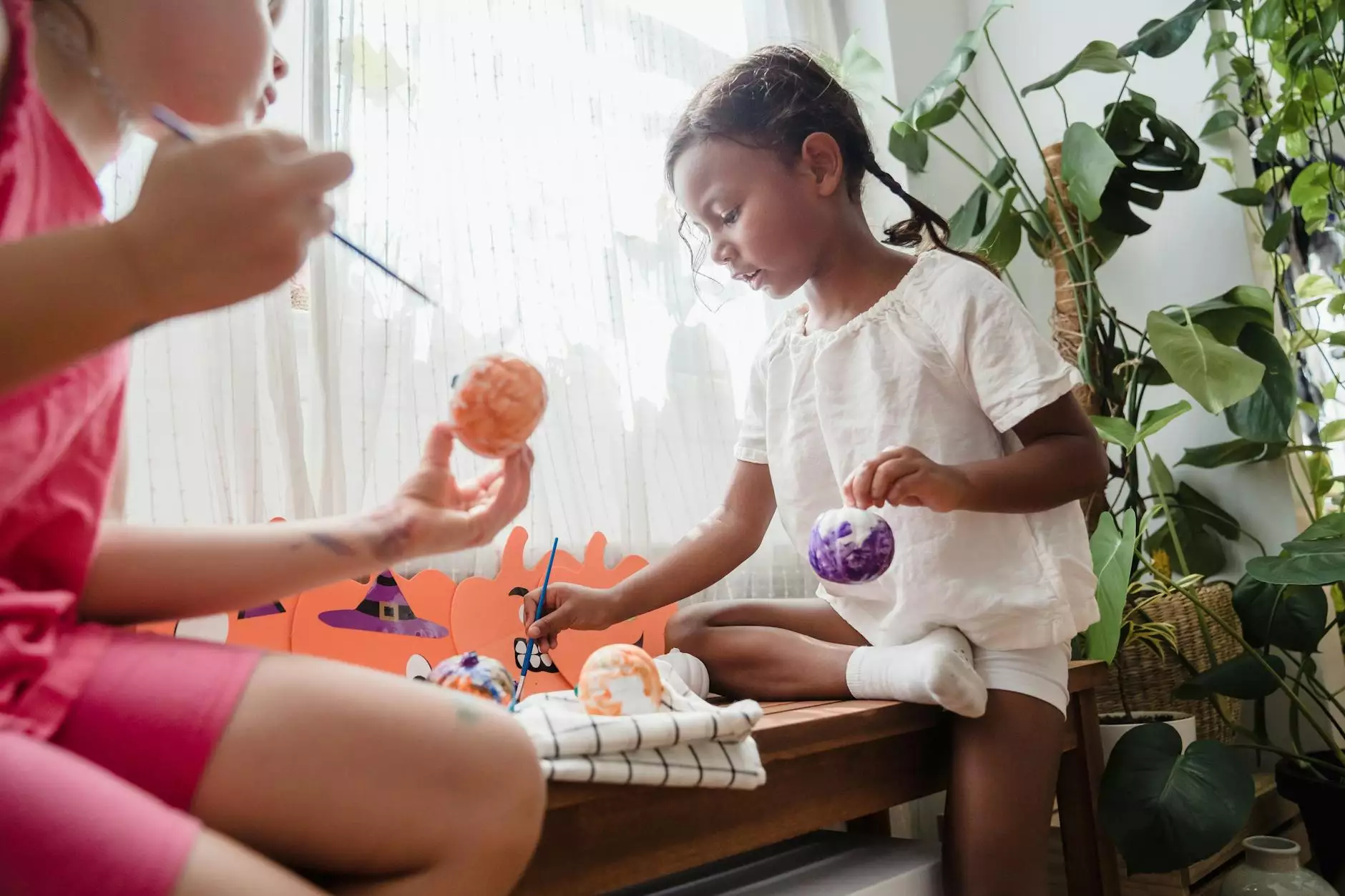
The automotive industry is a vast field, constantly evolving with advancements in technology and design. Among the significant developments is the use of automotive plastic parts. These components have become critical in enhancing vehicle performance, reducing weight, and improving fuel efficiency, all while catering to the aesthetic demands of modern consumers.
Understanding Automotive Plastic Parts
Automotive plastic parts include a wide range of components used in vehicles, from exterior panels to interior fittings. As an alternative to traditional metal parts, plastics offer several advantages such as lower weight, corrosion resistance, and greater design flexibility. The types of plastics commonly used include ABS (Acrylonitrile Butadiene Styrene), PP (Polypropylene), and PC (Polycarbonate), each serving unique roles in the automotive manufacturing process.
The Role of Plastics in Vehicle Manufacturing
Reducing weight is a crucial factor in the automotive industry, and this is where automotive plastic parts shine. Lighter vehicles require less energy to operate, which translates to better fuel efficiency and lower emissions. Moreover, the integration of plastics enables manufacturers to explore innovative designs that were previously unattainable with metals.
Key Benefits of Automotive Plastic Parts
- Weight Reduction: Plastics are significantly lighter than metal, which contributes to lower overall vehicle weight.
- Corrosion Resistance: Unlike metals, plastics do not rust or corrode, which enhances the longevity of automotive parts.
- Design Flexibility: Plastics can be molded into complex shapes, allowing for greater design innovation.
- Cost-Effectiveness: The manufacturing process of plastic parts is often less expensive than that of metal components, leading to cost savings for manufacturers.
- Improved Safety: Plastics can be engineered to absorb impact energy, potentially increasing passenger safety during collisions.
Manufacturing Processes of Automotive Plastic Parts
The production of automotive plastic parts involves several advanced processes, which include:
Injection Molding
Injection molding is the most prevalent manufacturing process for automotive plastic parts. In this technique, plastic granules are heated and injected into a mold, where they cool and solidify into the desired shape. This process is favored for its ability to produce high volumes of consistent and intricate parts at lower costs.
Blow Molding
Blow molding is primarily used for creating hollow plastic parts, such as fuel tanks and air ducts. In this process, a heated tube of plastic is inflated within a mold, forming a hollow shape. Blow molding is essential for creating lightweight components that are crucial for automotive applications.
Thermoforming
Thermoforming involves heating a plastic sheet until pliable, and then forming it into shape within a mold. This method is often used for larger parts, such as dashboards and door panels, where costs can be kept low by reducing waste material.
3D Printing
As technology advances, 3D printing is becoming increasingly popular for prototyping automotive plastic parts. This method allows for rapid prototyping and reduces the time between design and production, making it invaluable in modern automotive development.
The Impact of Automotive Plastic Parts on Sustainability
With an increasing focus on sustainability, the automotive industry is shifting towards eco-friendly practices. The use of automotive plastic parts plays a significant role in this transformation. Cars produced with lighter materials not only consume less fuel but can also incorporate recycled plastics, significantly reducing their ecological footprint.
Recycling and Reusability
Many automotive plastics are recyclable, making it possible to repurpose materials rather than disposing of them after vehicle life cycles end. This approach not only conserves resources but also reduces landfill waste, aligning with global sustainability goals.
Challenges in the Automotive Plastic Industry
Despite their benefits, automotive plastic parts are not without challenges. Some issues include:
- Material Limitations: Although durable, some plastics may not perform as well as metals in extreme conditions.
- Flammability: Certain plastics can pose a higher risk of fire, necessitating the development of flame-retardant materials.
- Environmental Concerns: The production of plastics can lead to pollution and depleting fossil fuels unless sustainable practices are adopted.
Future Trends in Automotive Plastics
The future of automotive plastic parts is bright, with several trends shaping their evolution:
Smart Plastics
Integration of technology will lead to smart plastics that can monitor vehicle performance or respond to environmental changes. For instance, automotive plastic parts embedded with sensors can provide data about temperature or stress, enabling preventive maintenance and improving safety.
Bio-based Plastics
As sustainability becomes a priority for manufacturers, bio-based plastics derived from renewable resources will likely see increased use in the automotive sector. These materials promise to reduce reliance on petroleum-based plastics and support green manufacturing initiatives.
Advancements in Composite Materials
Combining plastics with other materials, such as carbon fiber and glass fiber, can produce composites that offer enhanced strength-to-weight ratios, paving the way for even more innovative automotive plastic parts.
Final Thoughts
The role of automotive plastic parts in the automotive industry cannot be overstated. From metal fabricators like DeepMould.net creating specialized components to advances in recycling and sustainable practices, plastics are set to transform how vehicles are designed and manufactured. As we move forward, embracing innovations in plastic technology will be crucial for manufacturers looking to stay competitive and environmentally responsible.
In conclusion, the integration of automotive plastic parts not only enhances vehicle performance but also contributes to sustainability efforts across the industry. As technology progresses, the potential to innovate and improve these materials will shape the future of automotive design and production.