CNC Machining Parts Supplier: Elevating Manufacturing Standards
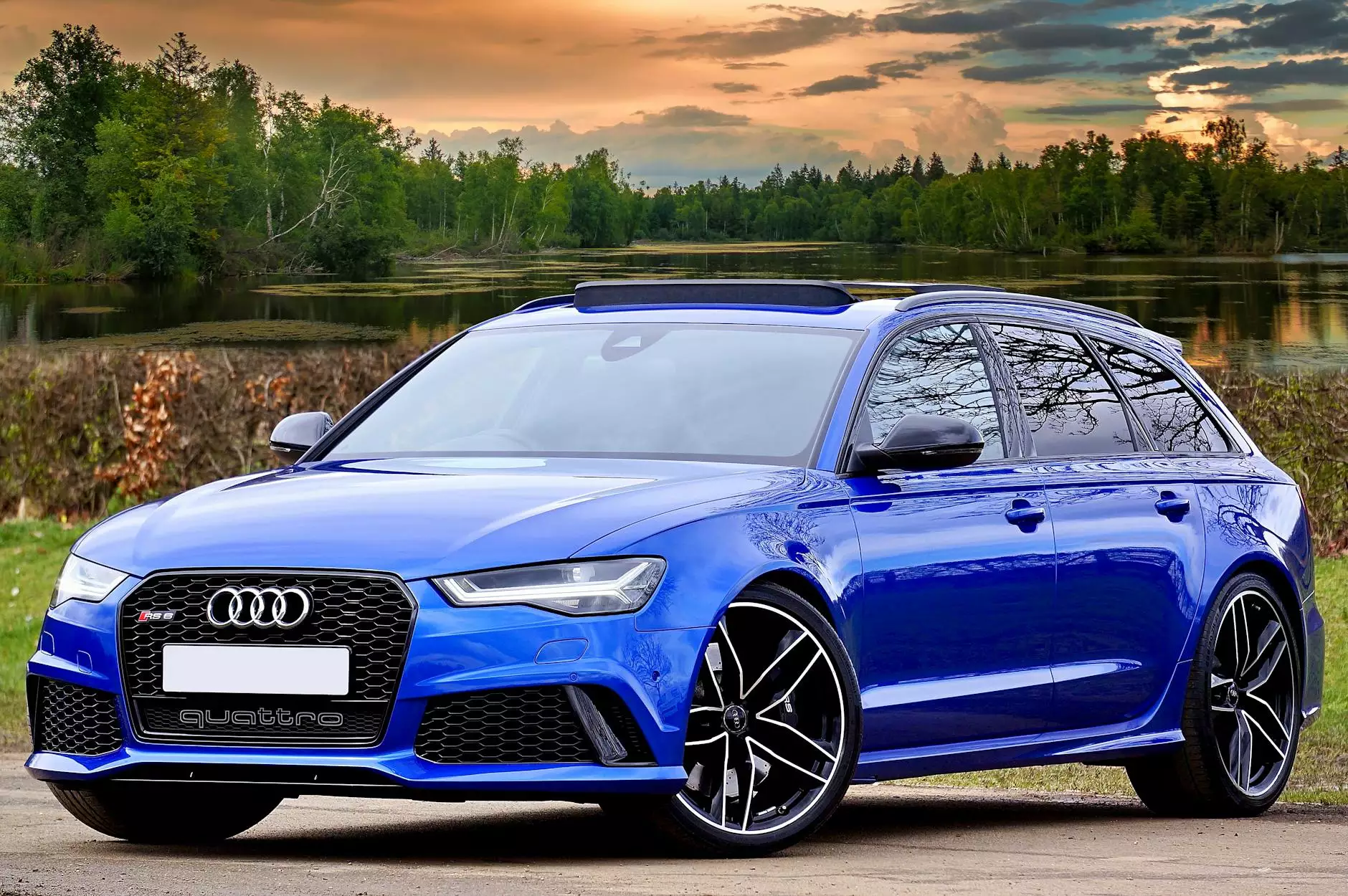
In the rapidly evolving landscape of manufacturing, the role of a cnc machining parts supplier has become increasingly pivotal. As industries bow to precision, efficiency, and cost-effectiveness, companies like DeepMould.net have emerged as key players in providing high-quality metal components through advanced CNC machining processes. This article delves into the world of CNC machining, exploring its relevance, advantages, and how it shapes the future of manufacturing.
Understanding CNC Machining
CNC (Computer Numerical Control) machining refers to the automated control of machining tools by means of a computer. It includes processes like drilling, milling, turning, and electrical discharge machining (EDM). This technology revolutionized the manufacturing sector by replacing manual operations with computer-driven solutions, thus vastly increasing production speed and accuracy.
The Importance of Choosing the Right CNC Machining Parts Supplier
When seeking a cnc machining parts supplier, several factors must be considered to ensure that the chosen partner can meet your specific needs.
1. Quality Assurance
The integrity of the finished product is paramount. A reputable supplier focuses on quality and employs stringent quality control measures throughout the production process.
2. Technological Capability
An adept cnc machining parts supplier should possess cutting-edge machinery and tools, often utilizing CAD (Computer-Aided Design) and CAM (Computer-Aided Manufacturing) systems to guarantee precision machining parts.
3. Experience and Expertise
Supplier experience is crucial. Understanding various materials, tolerances, and industry standards can significantly affect the project's outcome. The ideal supplier should have a proven track record in handling jobs similar to yours.
4. Flexibility and Customization
Today's market demands flexibility and specialization. A good supplier can provide custom machining solutions tailored to the specific needs of the client. This adaptability can significantly enhance the production process.
5. Communication and Support
Effective communication facilitates smoother operations. A reliable supplier should be responsive and provide comprehensive customer support during the entire manufacturing cycle.
Advantages of CNC Machining
The adoption of CNC machining brings numerous benefits to manufacturers and suppliers alike.
Increased Precision and Accuracy
One of the primary advantages of CNC machining is its unmatched precision. The technology minimizes human error and can consistently produce parts that adhere to tight tolerances, making it ideal for industries requiring exact specifications.
Enhanced Efficiency
CNC machines operate rapidly, allowing for high-volume production runs without the need for constant human intervention. This efficiency translates to faster turnaround times, essential in today's competitive market.
Cost-Effectiveness
By reducing waste material, labor costs, and production times, CNC machining significantly cuts down manufacturing expenses. Consequently, partnering with a cnc machining parts supplier can lead to considerable savings over time.
Versatility
CNC machining is capable of working with a myriad of materials, including metals, plastics, and composites. This versatility makes it a suitable choice across various industries, from aerospace to automotive and beyond.
Industries Benefiting from CNC Machining
Numerous sectors leverage the capabilities of CNC machining to improve their production processes and product quality.
- Aerospace Industry: Precision components are essential for aircraft safety and performance.
- Automotive Sector: Manufacturers require high-quality parts for engines and other systems.
- Medical Device Manufacturing: CNC machining guarantees sterile, precise tools and components.
- Electronics Industry: Intricate housings and components require high precision to function effectively.
- Energy Sector: Renewable energy technologies, such as wind turbine components, benefit from CNC machining capabilities.
CNC Machining Processes Explained
1. CNC Turning
This process involves rotating a workpiece against a cutting tool to shape it into desired dimensions. It is commonly used for cylindrical parts, such as shafts and bolts.
2. CNC Milling
CNC milling utilizes rotating cutters to remove material from a stationary workpiece, enabling the production of complex shapes and features. This process can produce both simple and intricate parts.
3. CNC Drilling
This process is specifically designed to create round holes in a material and is often integrated with milling processes to refine features or create multi-functional parts.
4. CNC Electrical Discharge Machining (EDM)
EDM is best suited for hard materials. It works by using electrical sparks to erode material, creating complex shapes and intricate details with high accuracy.
Conclusion: The Future of CNC Machining and Metal Fabrication
The landscape of manufacturing is undoubtedly changing, driven by the increasing demand for precision and quality. As a leading cnc machining parts supplier, DeepMould.net stands at the forefront of this revolution, offering innovative solutions tailored to various industries. With continuous advancements in technology, the future of CNC machining holds exciting prospects, ensuring that companies can meet and exceed customer expectations.
In summarizing the importance of CNC machining in contemporary manufacturing, it is clear that choosing the right supplier is vital. The benefits of enhanced precision, cost-effectiveness, and flexibility firmly establish CNC machining as a cornerstone of modern production.
Investing in quality machinery and partnering with a proficient supplier can transform a business's production capabilities, leading to increased competitiveness and long-term success. Explore further into CNC machining, and discover how to elevate your manufacturing standards today.