The Ultimate Guide to Die Casting Mold: Transforming Metal Fabrication
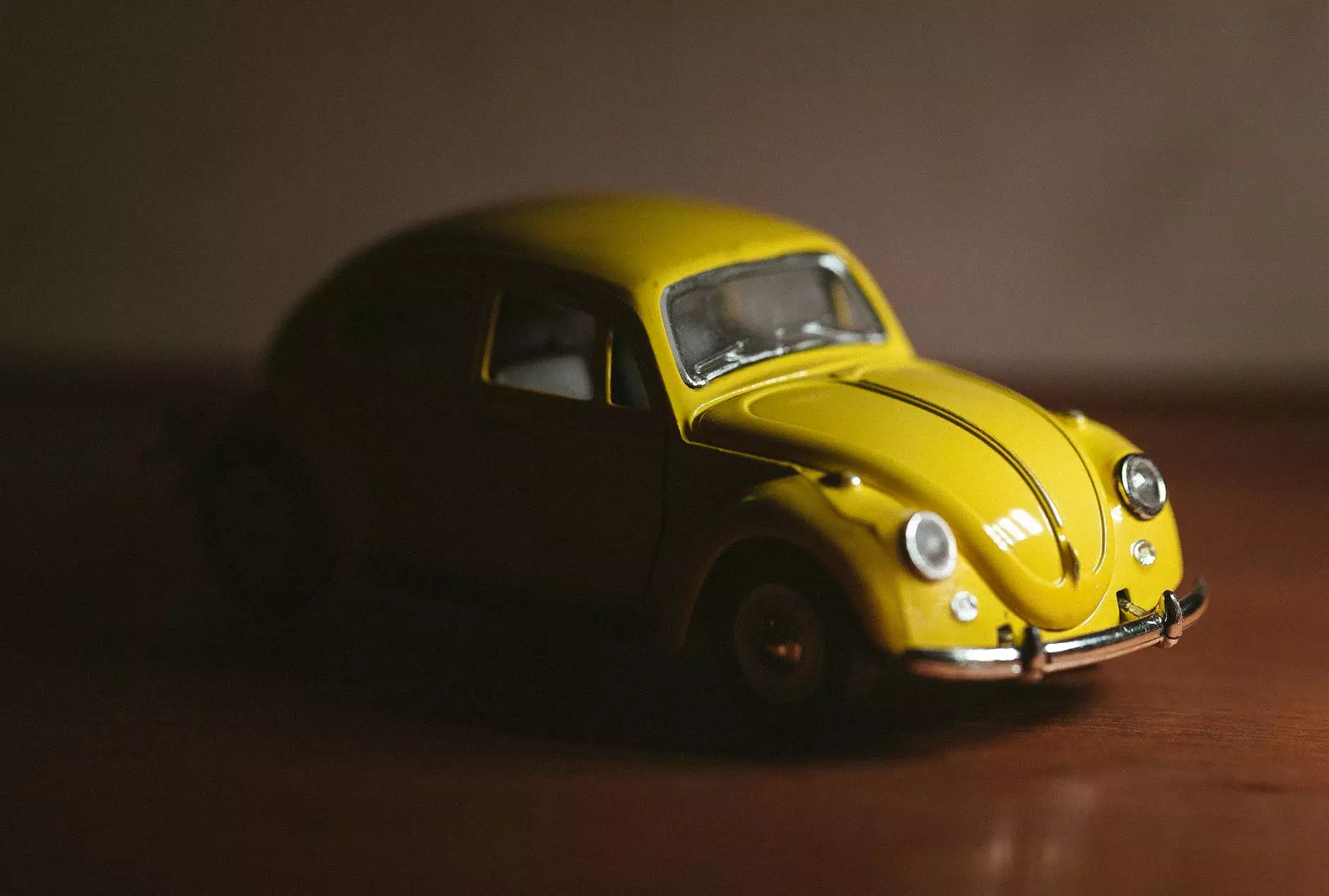
In the world of metal fabrication, few processes are as pivotal as the die casting method. Die casting molds serve as fundamental components in this process, allowing businesses to produce high-quality, durable, and intricate metal parts. This article aims to explore the intricacies of die casting molds, their significance in the metal fabrication industry, and how they can enhance manufacturing processes.
Understanding Die Casting: A Brief Overview
Die casting is a manufacturing process that involves forcing molten metal into a mold cavity. This process is renowned for its precision, repeatability, and ability to produce complex shapes with thin walls. The use of die casting molds is essential as they define the shape of the finished product, influence its geometry, and dictate the physical properties of the final components.
Key Advantages of Die Casting
The die casting process offers numerous advantages that make it a preferred choice for many manufacturers. Some of the most notable benefits include:
- High Precision: Die casting molds allow for tight tolerances, ensuring that parts fit together seamlessly and function without issues.
- Complex Shapes: The ability to create intricate geometries reduces the need for post-casting machining, saving time and costs.
- Durability: Die cast components exhibit excellent mechanical properties, making them suitable for various demanding applications.
- Efficiency: The rapid production cycle enables manufacturers to meet high demand without compromising quality.
The Role of Die Casting Molds in Metal Fabrication
At the heart of the die casting process lies the die casting mold. This mold is typically made from high-strength, thermal-resistant alloys designed to withstand the intense heat and pressure of the casting process. Here are some key aspects of die casting molds and their roles in enhancing metal fabrication:
1. Types of Die Casting Molds
There are two primary types of die casting molds used in the industry:
- Permanent Mold: These molds are reusable and made from metal, allowing for better heat conduction. They are ideal for high-volume production scenarios.
- Sand Mold: Made from sand and clay, these molds are often used for lower production volumes and offer more flexibility in design
2. Customization and Design
Custom die casting molds can be engineered to meet specific requirements. The design process involves collaboration with clients to understand their needs and the characteristics of the components being produced. Advanced software tools and techniques allow for simulations and optimizations to achieve the best results.
3. Material Selection for Molds
The choice of materials for die casting molds is critically important. Common materials include:
- Steel: Often used for its strength and durability, making it suitable for high-volume production.
- Aluminum: Lightweight and less expensive, aluminum molds are often used for lower production runs.
- Copper Alloys: Provide excellent thermal conductivity, which is beneficial when cooling the molds rapidly.
How Die Casting Molds Impact Production Processes
The efficiency and effectiveness of production processes are greatly influenced by the quality of die casting molds used. Here’s how:
1. Reducing Waste
High-quality die casting molds minimize material waste, as they are engineered to achieve precise dimensions. This efficiency not only lowers material costs but also reduces the environmental impact of manufacturing.
2. Enhanced Surface Finish
The surface finish of die cast products directly correlates to the quality of the mold. Superior molds can produce parts that require little to no additional machining, ensuring a smooth and aesthetically pleasing surface right out of the mold.
3. Increasing Production Rates
With the ability to produce multiple components simultaneously, die casting molds significantly enhance production rates. Mass production becomes feasible, thereby meeting market demand efficiently.
Applications of Die Casting Molds Across Industries
Die casting is employed across various industries due to its versatility and efficiency. Here are some industries that leverage die casting molds effectively:
- Automotive: Used for producing engine blocks, transmission cases, and various structural parts.
- Aerospace: Critical components like brackets, housings, and covers are crafted to meet stringent safety and performance standards.
- Electronics: Used for heat sinks, casings, and connectors that require durable and lightweight materials.
- Consumer Products: From kitchen appliances to sporting goods, die casting molds are used to create durable product parts.
The Future of Die Casting Molds and Metal Fabrication
As technology evolves, so does the die casting process. Advances in materials science, 3D printing, and computer-aided design are propelling the capabilities of die casting molds. The future is bright for businesses that leverage these innovations, leading to cost savings, higher quality products, and greater flexibility in production.
1. The Rise of 3D Printing
3D printing technologies are making their way into the die casting industry, allowing for rapid prototyping and the production of complex molds that were previously impossible to create. This reduces development time and costs, enabling companies to respond quickly to market changes.
2. Enhanced Automation
The integration of automation and robotics in die casting processes is set to revolutionize production lines. Automated systems can improve efficiency, decrease labor costs, and ensure consistent quality in the final products.
3. Sustainability Practices
With an increasing focus on sustainability, companies are researching ways to make die casting processes more environmentally friendly. This includes using recycled materials, optimizing energy consumption, and reducing emissions associated with production.
Conclusion: The Power of Die Casting Molds in Metal Fabrication
In summary, die casting molds are a cornerstone of efficient and effective metal fabrication. Their ability to produce high-quality, intricate components at scale positions them as an invaluable tool in various industries. As technology advances, businesses leveraging these molds can expect enhanced production capabilities, greater efficiency, and a stronger competitive edge in the marketplace. For businesses looking to explore the potential of die casting molds, consider partnering with experienced manufacturers like DeepMould.net, who can provide the expertise needed to succeed in today’s ever-evolving industrial landscape.